ANALYSIS OF RAW MATERIAL
By analyzing the raw materials, in accordance with the technical data sheet submitted by the supplier, the specifications are verified and the approval of each batch used in the production of foams can be ensured.
We take responsibility for our products. For this reason, Aramis Foams tests and is continually homologating all the foams in the laboratory before starting the foaming process in the factory. By analyzing the raw materials in accordance with the technical data sheet submitted by the supplier, the specifications are verified and the approval of each batch of raw materials used in polyurethane foams can be ensured.
Tested Parameters
- The amount of samples that are to be tested
- The density of raw and auxiliary materials in liquid form is determined in accordance with ASTM D 891 – 95
- The viscosity of raw and auxiliary materials in liquid form is achieved in accordance with ASTM D 4878 – 98
- The water content of polyether polyols is designed in accordance with ASTM E 203-01
- The acidity index for polyether polyols is performed in accordance with ASTM D 4662-03
- The NCO content of diisocyanates is designed in accordance with DIN 53185 (same device as in line 5)
- Hydrolyzable chloride from diisocyanates is designed in accordance with ASTM D 4663 -98 (same device as in line 5)
- The pH value of the water-based adhesive is determined in accordance with ASTM DIN 53785
- The solids content of the water-based adhesive is in accordance with ASTM DIN 11358
FINISHED PRODUCTS ANALYSIS
The inspection of the physical-mechanical characteristics of the polyurethane foam blocks is performed for each batch of foam after the maturation period in completed.
The values of each parameter analyzed must comply with the specifications of the IOS-MAT 0076 standard so that the batch of foam analyzed can be declared compliant and used in the next step of processing polyurethane foam blocks.
All the results obtained are centralized in an analysis bulletin and sent to the quality inspector.
Verified Parameters:
- The density is designed in accordance with the ISO 845 standard
- Hardness is achieved through indentation in accordance with the ISO 2439 standard; Traction endurance and breaking point elongation are achieved in accordance with the ISO 1798 standard
- Elasticity (resilience) is achieved in accordance with the ISO 8307 standard (4)
- The recovery time after compression (recovery time) is applied only for viscoelastic foams (memory foams) and is designed in accordance with the IKEA IOS-MAT-0076 standard
- The relative deformation due to compression is performed in accordance with the ISO 3386 standard
- Remaining deformation is performed in accordance with the ISO 1856 standard
RESEARCH & DEVELOPMENT
In the production of polyurethane foams we use raw materials obtained from renewable resources for environmental protection.
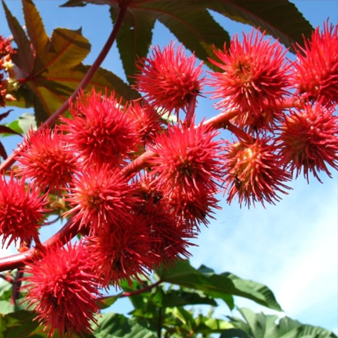
POLYURETHANE FOAMS – BIO
Odorless and low emission polyurethane foams
Benefits:
- Castor and soybean oils are used as raw materials
- Up to 25% renewable plant material content
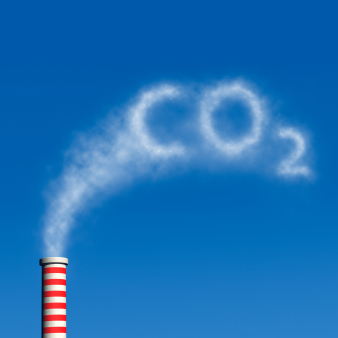
POLYURETHANE FOAMS BASED ON POLYOL WITH CO2
Low emission standard polyurethane foams
Benefits
- Resource preservation by saving petroleum and using resources from new raw material
- Climate protection by using CO2, thus avoiding CO2 emissions
FOAM PRODUCTION
The QFM foaming installation is equipped with fully automated dosing lines that allow the synthesis of PU foams according to the ISO quality-environment requirements of the automotive industry and upholstered furniture.
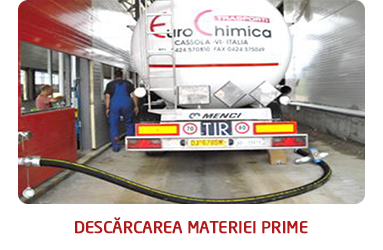
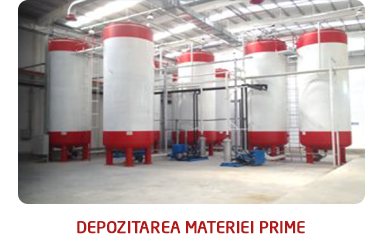
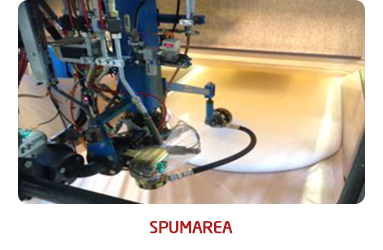
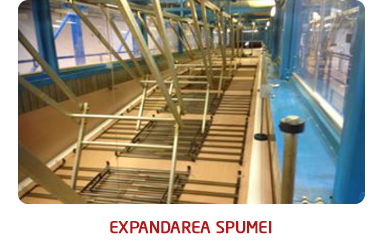
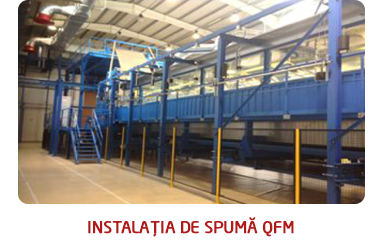
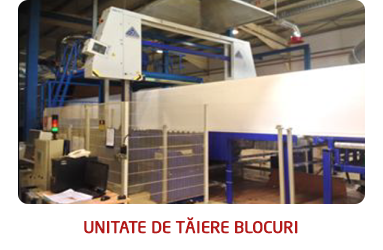
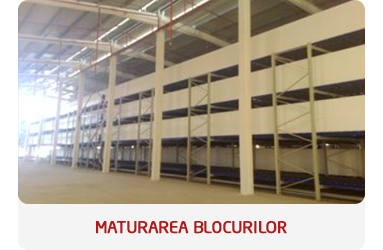
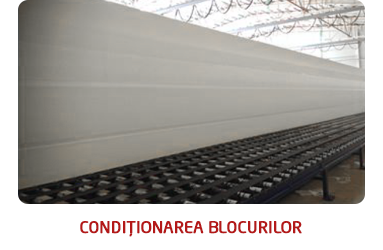
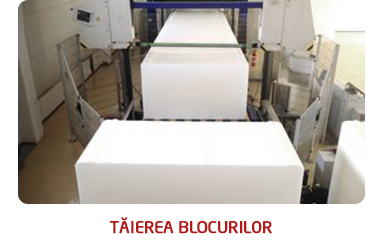
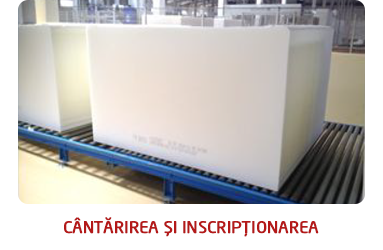
COMPUTERIZED ASSISTANCE FOR ALL EQUIPMENT PARAMETERS
- It is advantageous for the continuous assurance of the reproducibility and traceability of the technological process.
- The high degree of homogenization of the reaction mixture is achieved with the help of a mixing head recently developed and patented by German specialists.
THE ADVANTAGES OF THIS NEW TECHNOLOGY
- perfect mix and homogenization of raw and auxiliary materials used in the recipe
- laminar deposit of the reaction mixture
- control of cellular structure for the PU foam from fine to rough during production
- organic solvents removal for washing and cleaning the mixing head
ATTAINMENT OF THE ENTIRE RANGE OF PU FOAMS WITH EXCELLENT PHYSICAL AND MECHANICAL QUALITIES
- perfect mix and homogenization of raw and auxiliary materials used in the recipe
- laminar deposit of the reaction mixture
- control of cellular structure for the PU foam from fine to rough during production
- organic solvents removal for washing and cleaning the mixing head
POLYURETHANE FOAMS PROCESSING
The complexity of the shape of a polyurethane foam part is faithfully respected by its design with the help of a digitizing equipment connected to a system computer that processes the final shape of the article in three dimensions.
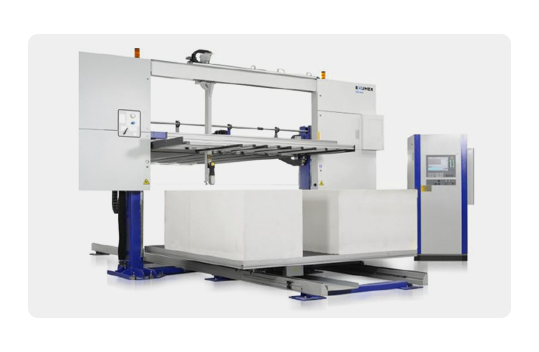
The automatic cutting of short blocks is done with the help of a guillotine-type of blade at an optimal size to minimize technological losses and generated waste.
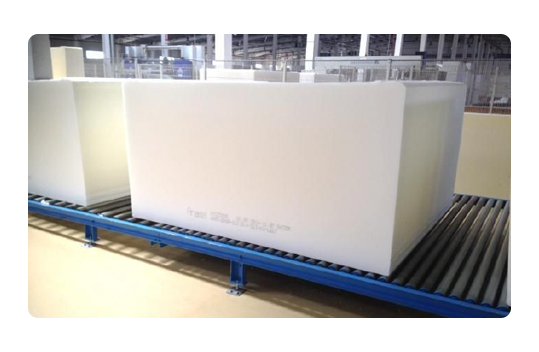
Depending on the size and shape, the short blocks are to be processed on different lines or CNC cutting machines, all automated and equipped with state-of-the-art German technology.
THEY LEAD TO PROCESSING CAPABILITY
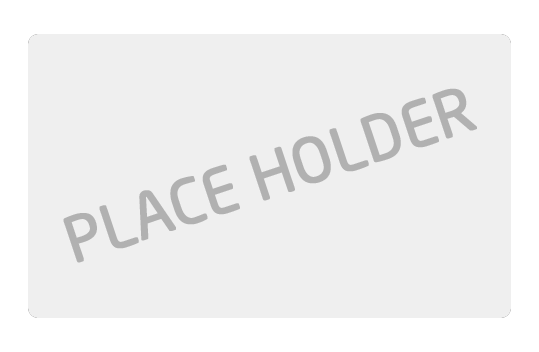
3D shaped polyurethane foam indicator.
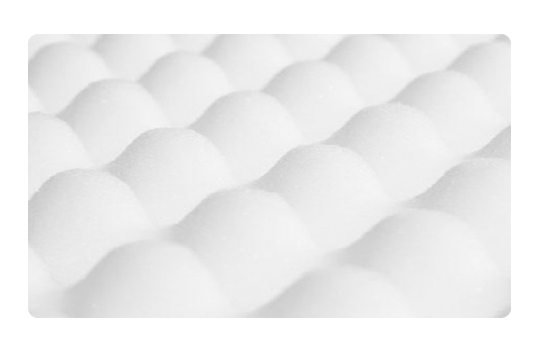
Polyurethane foam boards with „egg framing" shape
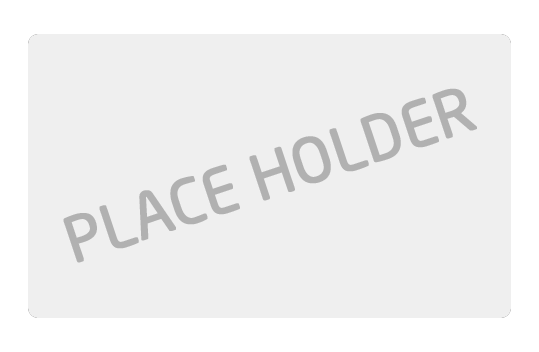
Polyurethane foam boards
MATTRESS PRODUCTION
Using the raw product, through the actions mentioned above, we can develop into finished product foam mattresses, those with bi-conical springs (bonell) and also with individually wrapped springs (pocket).
FOAM MATTRESSES

The core of the foam mattresses consists entirely of conventional polyurethane foam and / or high resilience polyurethane foam. Thanks to advanced polyurethane foam processing technology, the core can be processed so that the mattress transforms a classic one into a comfort zones mattress.
The advanced technology of polyurethane foam production allows the mattress core to be improved with extra comfort. The comfort of the mattress is obtained by adding a layer of viscoelastic foam (memory) or latex foam like by gluing them with ecological adhesive.
SPRING MATTRESSES
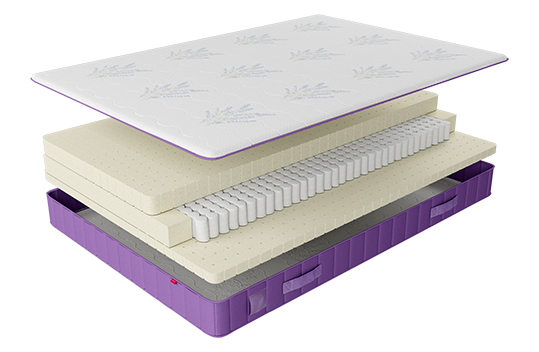
Pocket spring mattresses are based on the core consisting of individually wrapped helical springs embedded in a frame made of polyurethane foam.
The production of spring mattresses is carried out with the help of an automated production line that ensures a linear cadence and a rigorous control of productivity and quality.
For added comfort, a layer of viscoelastic foam or latex-like foam is added to the core of the spring mattress.
TOPPER MATTRESSES
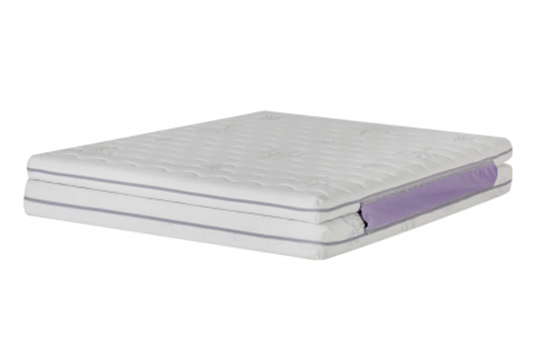
The interior of the topper mattresses consists entirely of high resilient polyurethane foam, viscoelastic foam (memory) or latex like foam depending on your preferred comfort. Thanks to advanced foam processing technology, they can be processed so that the topper mattress transforms a classic mattress into a mattress with different types of comfort. Provides a sleep-reducing pressure effect due to the uniform distribution of weight over the entire surface of the mattress.
MATTRESS PACKAGING
Mattress packaging is done with press and roll technology for easy handling and transport.
Foam is a material that returns to its original shape. However, after a period in which the mattress has been kept rolled, it takes up to 72 hours to return to its original cellular structure.
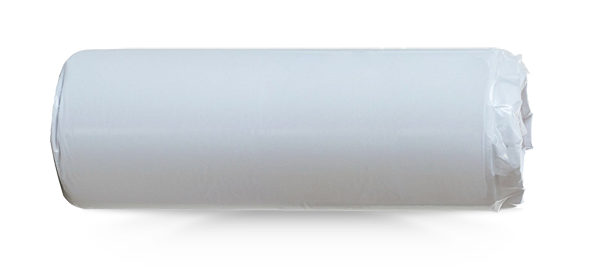